Injection Molding of Plastics: A Comprehensive Guide for Metal Fabricators
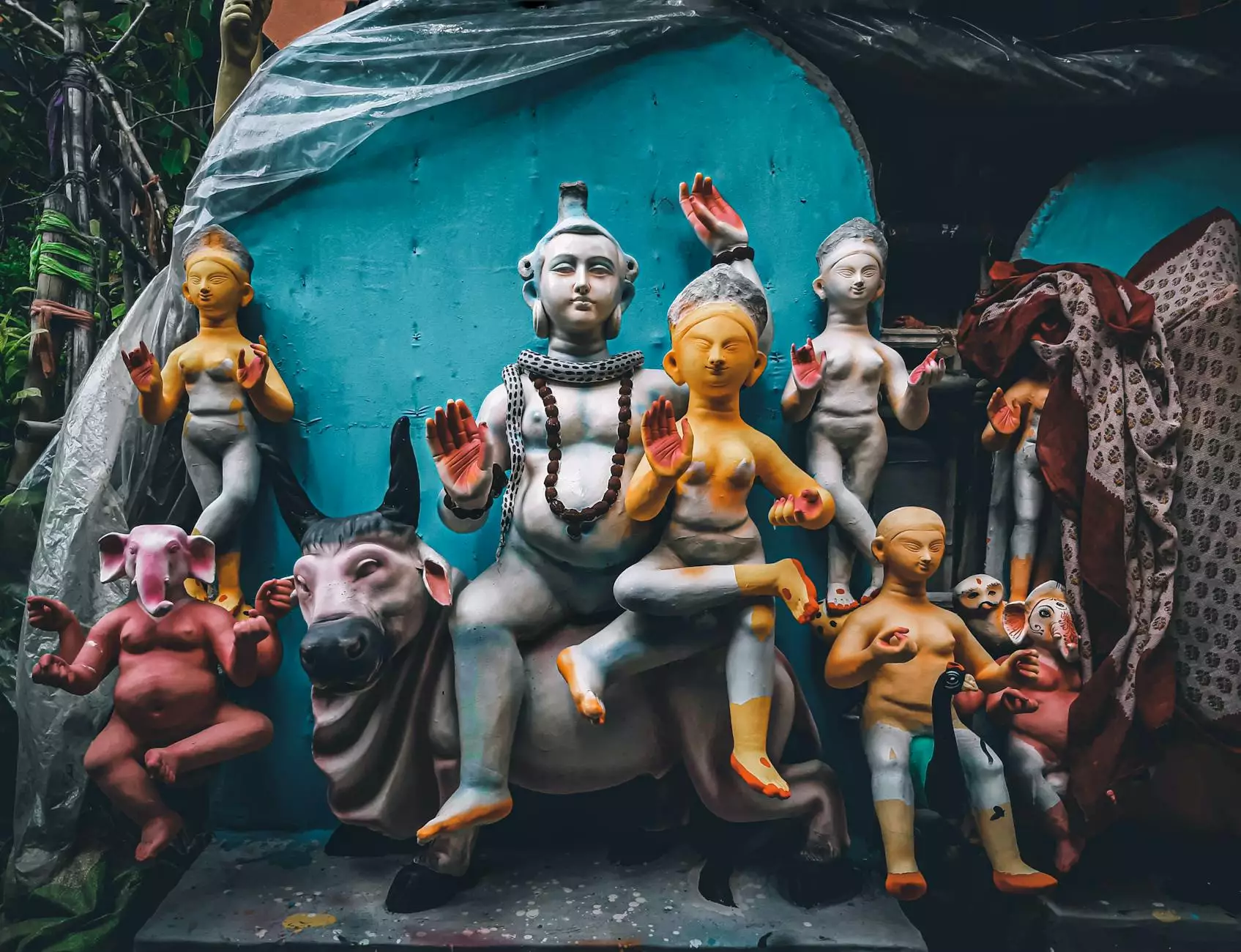
Understanding Injection Molding of Plastics
Injection molding of plastics is a sophisticated manufacturing process that is widely utilized in the production of plastic components ranging from intricate parts to large structural items. This method is not only efficient but also highly effective in producing consistent, complex shapes with minimal waste. As the manufacturing industry increasingly turns its focus towards efficiency, precision, and sustainability, understanding this process has become essential for metal fabricators who aim to integrate plastic components into their offerings.
How Injection Molding Works
The injection molding process involves several key steps:
- Material Preparation: The first stage involves the preparation of the plastic resin, which is typically in the form of pellets.
- Heating and Melting: The pellets are fed into a heated barrel where they are melted into a viscous liquid. This step requires precise temperature control to ensure the material reaches the right viscosity.
- Injection: The molten plastic is injected into a mold under high pressure. This pressure ensures that the mold cavity is completely filled, capturing all details of the mold's design.
- Cooling: After the mold is filled, the material is allowed to cool and solidify, forming the final product.
- Demolding: Once cooled, the mold is opened, and the finished plastic part is ejected.
This systematic approach allows for high-volume production runs and can be easily adjusted to accommodate different plastic materials and part designs.
Benefits of Injection Molding for Metal Fabricators
Incorporating injection molding of plastics into your product offerings can yield numerous advantages for metal fabricators:
- Efficiency: Injection molding is known for its speed, making it possible to produce thousands of identical parts in a short time frame.
- Cost-Effectiveness: While the initial setup costs can be high due to mold fabrication, the long-term production costs decrease significantly due to reduced material waste and lower labor costs.
- Design Flexibility: The process supports complex designs and can produce intricate details that might be challenging to achieve through traditional metal fabrication methods.
- Material Variety: A wide range of plastic materials can be used, allowing for flexibility based on the required properties of the final product.
- Reduced Waste: The precision of injection molding minimizes excess material, thus promoting a more sustainable manufacturing approach.
Applications of Injection Molding in Metal Fabrication
Injection molding plays a pivotal role in various sectors where metal fabricators produce plastic components or products. Here are key applications:
- Automotive Industry: Components like dashboards, bumpers, and trim pieces.
- Consumer Electronics: Casings for phones, tablets, and other devices.
- Medical Devices: Parts that require strict compliance with health regulations, such as syringes and housings for diagnostic equipment.
- Household Products: Items like kitchen utensils, storage containers, and toys.
- Industrial Components: Gears, housings, and other functional parts used in machinery.
Choosing the Right Material for Injection Molding
Selecting the appropriate material is crucial for the success of the injection molding of plastics process. Common materials used include:
- ABS (Acrylonitrile Butadiene Styrene): Known for its toughness and impact resistance.
- Polycarbonate: Noted for its transparency and high strength, often used in optical applications.
- Polypropylene: Lightweight and resistant to chemical solvents, ideal for automotive and consumer goods.
- Nylon: Excellent wear resistance and chemical resistance, thus commonly used in mechanical parts.
- Polystyrene: Used for less demanding applications where cost is a significant concern.
The choice of material will influence the mechanical properties, aesthetics, and overall performance of the final product.
Design Considerations for Injection Molding
When designing parts for injection molding of plastics, several factors must be taken into account to ensure manufacturability:
- Draft Angles: Incorporating draft angles on vertical surfaces helps in the demolding process.
- Wall Thickness: Uniform wall thickness is critical to avoid issues like warping and uneven cooling.
- Radii and Fillets: Adding rounded edges can improve the strength of the part and ease the flow of the molten material.
- Mold Design: The design must facilitate proper cooling and allow for easy assembly and disassembly.
- Texturing and Finishing: Surface finishes can be added to achieve desired appearances and functionalities.
Challenges in Injection Molding
While injection molding offers numerous benefits, there are also challenges that metal fabricators should be aware of:
- High Initial Costs: The cost of designing and fabricating molds can be significant.
- Material Limitations: Not all plastics are suitable for every application, limiting design choices.
- Machinery Requirements: Advanced machinery is necessary for precision molding, which can require significant investment.
- Production Revisions: Making changes to a molded part can be costly if modifications are needed after the mold has been created.
Future Trends in Injection Molding of Plastics
The injection molding industry is constantly evolving. Here are some trends that are shaping its future:
- Increased Automation: Emphasizing efficiency and reducing labor costs through automation of the injection molding process.
- 3D Printing Integration: Using 3D printing technologies for rapid prototyping and mold creation.
- Biodegradable Plastics: A shift towards sustainable materials that reduce environmental impact.
- Smart Manufacturing: Implementing IoT and AI in monitoring and optimizing production processes.
Conclusion
In summary, the injection molding of plastics offers metal fabricators an exceptional opportunity to enhance their product lines and improve manufacturing efficiency. By understanding the processes, applications, and challenges associated with injection molding, businesses can make informed decisions that will advance their manufacturing capabilities.
As the industry continues to innovate, staying informed about new materials, technologies, and techniques will be crucial for metal fabricators aiming to remain competitive in the evolving manufacturing landscape. By embracing these advancements, your business can not only meet the demands of modern production but also position itself at the forefront of the manufacturing sector.
For Further Information
For more insights into the injection molding of plastics and how it can benefit your business, please visit deepmould.net for detailed resources and support.